

First article inspection of dimensions, form, and shape are rounded up by the ability to qualify and quantify injection molding defects such as porosity and inclusions as well as fiber orientations and volume fractions. Dimensional analyses of simulation models can help to find the best parameter set as an input for the first mold. Designed and simulated different rigging systems to arrive at an optimum system satisfying velocity, air entrapment, microporosity as the major parameters using MagmaSoft Quantitative. A typical CAD model will accurately describe the shape and structure, but often also contain.
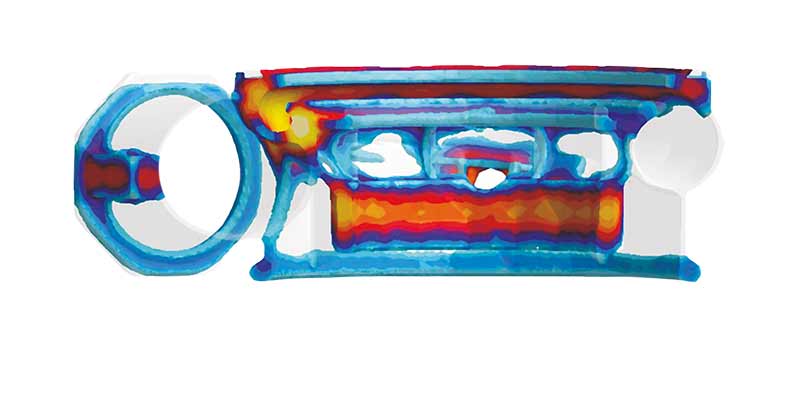

This geometry is represented via a CAD model. Volume Graphics supports all phases of injection molding from part design and process simulation to inline inspection. A good finite element analyst starts with both an understanding of the physics of the system that is to be analyzed and a complete description of the geometry of the system. This role will conduct material tests to control and optimize manufacturing. This position is responsible for monitoring, controlling and improving production processes to improve casting quality.
#MAGMASOFT SYSTEM REQUIREMENTS FULL#
Full volume measurement provides the quickest possible path from design to manufacturing. Position Summary:This administrative and technical position resides in the Foundry Operations and plays an integral role in maintaining and advancing the technical capabilities of Columbia Steel.
Surface characteristics such as color, transparency, or reflectivity are no problem for CT scanners. Consequently utilizing the methodology of virtual Design of Experiments and Autonomous Optimization, robust process parameters and optimized casting layouts can be established for all. Solid mechanical engineering experience engineers components and systems with little. MAGMASOFT is the comprehensive and effective optimization tool for improving metalcasting quality, optimizing process conditions and reducing production costs. CT gives you true insights such as the detection and analysis of injection molding defects, and the ability to acquire all dimensions even inside the parts. Provide dynamic design guidelines and requirements to mechanical. It does not stop at surface data from easily accessible geometries, which also conventional coordinate measuring machines (CMM) or optical scanners deliver. Computed tomography (CT) measurements provide the unique ability to get a full understanding of a part's quality.
